Indonesia Furniture Manufacturers Things To Know Before You Buy
Indonesia Furniture Manufacturers Things To Know Before You Buy
Blog Article
How Indonesia Furniture Manufacturers can Save You Time, Stress, and Money.
Table of ContentsExcitement About Indonesia Furniture ManufacturersGetting The Indonesia Furniture Manufacturers To WorkThe 6-Minute Rule for Indonesia Furniture ManufacturersExamine This Report on Indonesia Furniture ManufacturersIndonesia Furniture Manufacturers - Truths
There are some downsides to getting from a furniture manufacturer. A furniture seller is a firm that offers furniture made by various makers.When you purchase from a furniture seller, you're buying a furniture that's currently been made and prepares to be delivered to your home. One of the advantages of buying from a furniture store is that you can typically see and touch the item before you buy it.
At BH Furnishings, our team believe in establishing brand-new requirements for excellence in the production of business furnishings - Indonesia furniture manufacturers. Our dedication to innovation has led us to accept cutting-edge automation innovation, transforming the means we make furnishings and thrusting us to the forefront of the sector. Gone are the days of manual work controling the production floor
Our equipment works perfectly, assisted by the specific specifications established by our proficient engineers, ensuring constantly high-quality result. Bid farewell to manufacturing hold-ups and overtime expenses. Our automated systems operate relentlessly, 24/7, ensuring a consistent and continuous workflow. This indicates we not only satisfy but surpass delivery target dates, supplying our clients with a degree of dependability that traditional manufacturing methods just can't match.
Indonesia Furniture Manufacturers Fundamentals Explained
Our manufacturing ability has skyrocketed, enabling us to satisfy the needs of also the biggest tasks without endangering on quality. As your partner in industrial furniture options, we can effortlessly scale our outcome to suit your requirements, no issue the range. While typical manufacturing counts greatly on manual work, our automated systems have considerably lowered our reliance on a huge labor force.
Furnishings production is a complicated process that includes different stages, from designing and product option to manufacturing and assembly. At each phase, there is an opportunity of flaws or errors that can compromise the high quality of the last item. To make certain that furnishings is of premium quality, furniture manufacturers apply top quality control procedures to determine and rectify any kind of issues that may emerge throughout manufacturing.
The examination procedure ought to cover numerous aspects, such as setting up, surface, colour, design, product packaging, labelling, and marking. By implementing a strenuous evaluation process, producers can ensure their items meet the essential quality, safety, and resilience needs. They likewise supply the adaptability to attend to issues and make improvements before finishing the final item.
The process starts with the basic materials examination to the final setting up of the furniture. The goal is to make certain that the products are cost-free of issues, risk-free, and fulfill the customer's assumptions. Furnishings quality criteria are sets of guidelines and demands for furnishings production. They specify the needed quality level of furnishings production and cover aspects such as security, toughness, strength, and environmental impact.
The Main Principles Of Indonesia Furniture Manufacturers

To ensure their furnishings items can withstand different weather condition components, consisting of sun, rainfall, snow, and wind, makers need to think about internationally recognized criteria that comprise inspections and screening. Right here are some of the standards to bear in mind: ASTM F1561-03 is a worldwide conventional established by the American Section of the International Association for Screening Materials (ASTM).
UL 962 is an international safety and security requirement developed by Underwriters Laboratories (UL), an independent worldwide supply safety and security services company. The common applies to home and industrial furnishings, consisting of outdoor furniture.
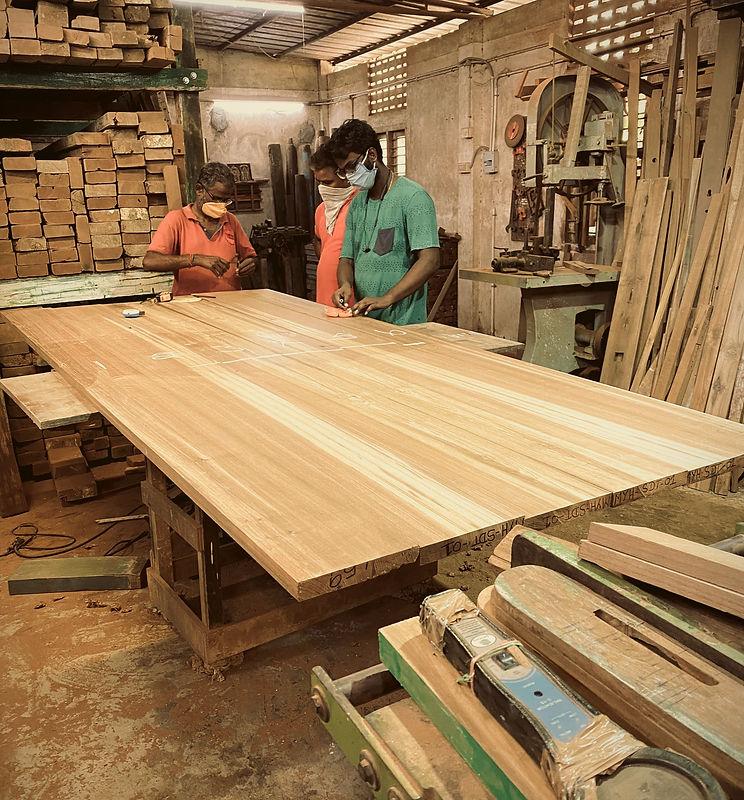
A Biased View of Indonesia Furniture Manufacturers
It helps to determine Your Domain Name issues in the furniture and assess its efficiency and conformity with the required high quality criteria. These examples generally represent the different types of furnishings that they generate.
This might entail a combination of different tests, including toughness screening, durability screening, safety screening, and environmental influence testing. The samples are then evaluated for numerous top quality parameters, such as strength, resilience, security, and environmental impact. The results are then assessed to identify whether the products satisfy the needed high quality requirements.

Usually, every retail shop furniture is various. All projects have concerning a month's time between layout ideation and final production. This is where the major obstacle exists. Layouts meeting client benefit Taking full advantage of space use in storage, screen, footfall, guest seating and pathways Guaranteeing convenience of access to items for trials and purchase Creating modular furniture that is simple to move and renovate Fulfilling safety requirements of customers A quick TAT from layout to manufacturing and setup with very little mistakes can help attend to the above problems.
What Does Indonesia Furniture Manufacturers Do?
A designer can comprehend the market fads and be prepared with ingenious styles ahead of time. Read below: basics Just How DriveWorks Aids You to Lower Lead Time in Production Designers usually have to alter the shapes and sizes of furnishings at a moment's notice. These may have various visual and practical demands like front workdesk, and maintenance workdesk that vary in dimensions.
on a common platform. This integration of sales and ERP functions brings more presence on price and pricing. It essentially passes on CPQ like functionality and enables generating quick quotes and quantities for spending plan assessments and completing orders. Indonesia furniture manufacturers. DriveWorks can auto-generate manufacturing store drawings with BOMs and DXFs for sheet cutting and boxing
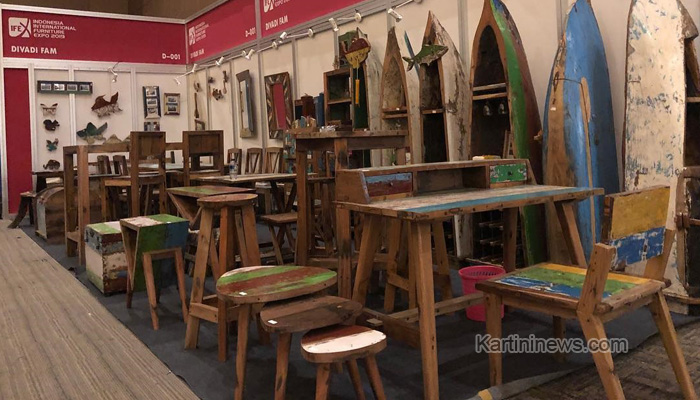
It is an extremely affordable market, with services making every effort to keep up with transforming consumer demands and the newest technical patterns. Today's consumers are a lot more most likely to favor furniture that is personalized and made with sustainable materials.
Report this page